2ndAmendmentNut
Member
At the request of several members, both here and over at Cast Boolits, I put this tutorial together to show my experiences with slow rust bluing. Slow rust bluing is a process that actually rusts your gun in a way to protect it. Pretty scary sounding, but the end results are beautiful. Rust bluing is also very cost effective and best used on those guns that might not necessarily warrant a professional reblue.
First up the victim. She is a S&W 10-10 police trade in that I purchased through Bud's about 3 or 4 years ago.
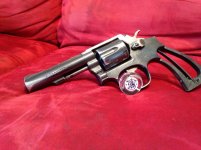
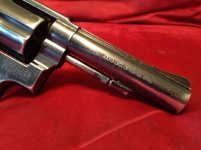
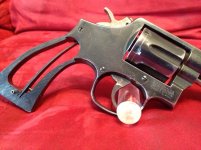
As you can see she was no beauty queen but certainly didn't deserve one of those nasty spray or baked on finishes.
Step one: Complete disassembly. For those nervous about disassembling a S&W do yourself a favor and pick up a copy of Mr. Kuhnhausen's excellent book. Also be sure to have all the proper tools.
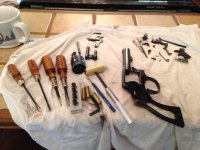
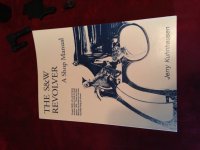
First up the victim. She is a S&W 10-10 police trade in that I purchased through Bud's about 3 or 4 years ago.
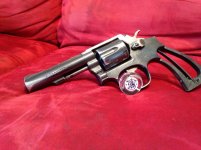
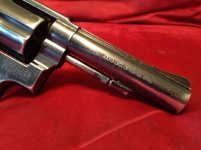
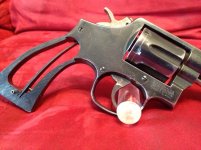
As you can see she was no beauty queen but certainly didn't deserve one of those nasty spray or baked on finishes.
Step one: Complete disassembly. For those nervous about disassembling a S&W do yourself a favor and pick up a copy of Mr. Kuhnhausen's excellent book. Also be sure to have all the proper tools.
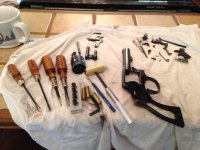
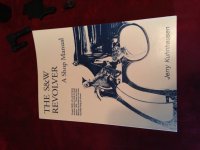
Last edited: